Swing Check Valve VS Wafer Check Valve.
In industrial product procurement, both swing check valves and wafer check valves play important roles, but there are significant differences between them.
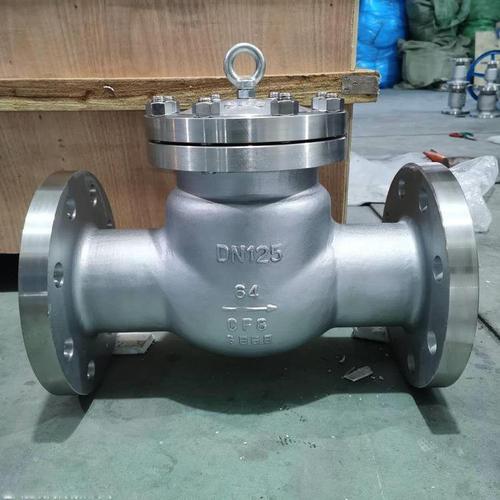
Swing check valve vs wafer check valve: main differences.
Structure.
Swing check valves: They have a hinged disc that swings open to allow forward flow and closes under reverse flow. They usually have a relatively large and bulky structure, often with a body that can be flanged at both ends for connection to pipes.
Wafer check valves: These are designed to fit between two flanges in a pipeline. They are much more compact and have a thinner profile compared to swing check valves.
Installation.
Swing check valves: Require more space for installation due to their larger size. They can be installed in both horizontal and vertical pipelines, but proper orientation is crucial for the hinged disc to function correctly.
Wafer check valves: Ideal for applications where space is limited. They are easily installed between standard pipe flanges and can be used in horizontal or vertical pipelines as well.
Performance.
Swing check valves: Tend to have a slower closing speed, which might cause water hammer in some high-flow or rapidly changing flow applications. However, they can handle high-flow rates and are suitable for large-diameter pipes.
Wafer check valves: Close rapidly, effectively reducing the risk of water hammer. They generally have lower pressure drops but may have limitations in handling very high-pressure or high-temperature applications compared to swing check valves.
Cost.
Swing check valves: Usually more expensive because of their larger size and more complex construction.
Wafer check valves: Are generally more cost – effective due to their simpler and more compact design.
Applications.
Swing Check Valve: It is suitable for high-pressure and high-temperature media, and is particularly applicable to large-diameter scenarios with low flow velocity and little change in the flow state. It is not suitable for pulsating flow, and its sealing performance is slightly inferior to that of the lift check valve.
Wafer Check Valve: It is more suitable for low-pressure and low-temperature occasions. With a simple structure, it is convenient for maintenance. It is suitable for large-diameter pipelines, but it is not advisable to be used in working conditions with high pressure or pulsating media.
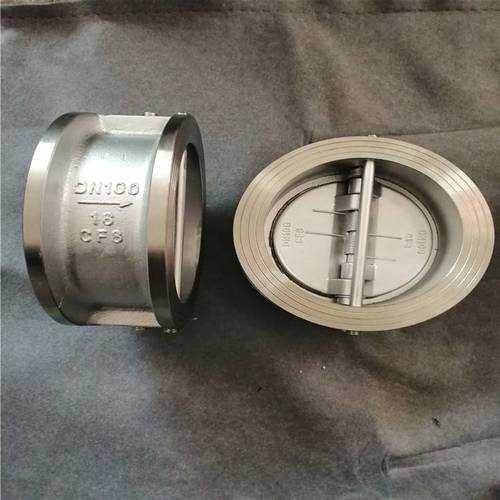
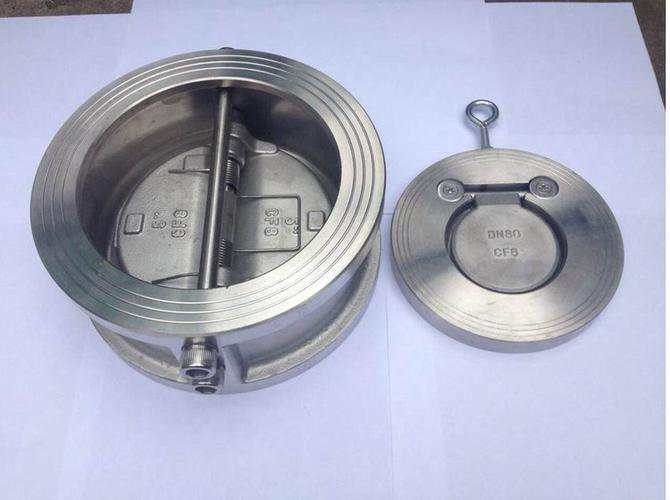
Special Precautions: wafer check valve vs swing check valve.
Wafer Check Valves.
- Compared with swing check valves, they have a larger flow resistance and are not suitable for use at the outlets of high-pressure (Class 900 and above) pumps and compressors.
- Due to the larger flow resistance compared to swing check valves, they are not suitable for applications with pulsating media.
- They have a larger flow resistance than swing check valves and exist a “target-hitting” phenomenon, so they are not suitable for oxygen media applications.
- Owing to the wafer type connection structure, they are not suitable for large-diameter (DN 600 and above), high-pressure (Class 900 and above) applications.
- Since they are equipped with a spring-assisted reset structure, for working conditions with low-pressure media, the spring stiffness should be specially set, and the crack pressure should be specified.
- They are not suitable for applications with severe scouring.
- They should be installed horizontally whenever possible. When used in vertical pipelines, the medium flow direction should be from bottom to top.
Swing Check Valves
- They should be installed horizontally whenever possible. When used in vertical pipelines, the medium flow direction should be from bottom to top.
- Due to structural limitations, they are not suitable for use in pipelines with a diameter of DN 40 or less.
- For large-diameter pipelines (e.g., DN 400 and above), tilting swing check valves are recommended.
- For working conditions with unstable pressure or flow, or pulsating media, and when the valve diameter is DN ≥ 200, tilting swing check valves are recommended.
In conclusion, both the swing check valve and the wafer check valve have their own characteristics. One needs to make a selection according to the specific application scenarios and pay attention to the correct usage and maintenance.