Floating Ball Valve vs Trunnion Ball Valve: A Comprehensive Comparison
In the world of industrial valves, the floating ball valve and the trunnion ball valve stand out as two widely-used types. These valves are essential for regulating fluid flow in industries such as oil and gas, chemical processing, and water treatment. Understanding their differences in detail is import for one to make the best decisions in valve selection for various applications.
The significant differences between floating ball valves and the trunnion ball valves can be compared in servial aspects.
Differences in Structure.
Floating Ball Valves: The ball is in a floating state within the valve body. There is no lower fixed shaft, and usually, only one upper valve stem is connected to the ball. This design makes the structure of the floating ball valve relatively simple, with a smaller volume and lighter weight.
Trunnion ball valves: The ball is fixedly connected to the valve body through the upper and lower valve stems. There is a fixed shaft at the bottom of the ball, and the ball can only rotate around the axis of the valve stem and cannot move freely within the valve body. The structure of the trunnion ball valve is relatively complex, with a larger volume and heavier weight.
Differences in Working Principle.
Floating Ball Valves: It relies on the pressure of the medium to push the ball, causing the ball to displace and press tightly against the sealing surface at the outlet end, thus achieving sealing. When closed, the greater the medium pressure, the better the sealing effect. However, when the pressure is low or there is no medium pressure, the sealing performance may be affected.
Trunnion ball valves: Through the pre-tightening force between the ball and the valve seat and the transmission of the valve stem, the ball is closely attached to the valve seat for sealing. Regardless of the high or low pressure of the medium, its sealing performance is relatively stable and is not affected by the fluctuation of the medium pressure.
Differences in Sealing Method.
Floating Ball Valves: Sealing depends on the medium pressure pushing the ball to press tightly against the valve seat at the outlet end, and the sealing effect is greatly affected by the medium pressure.
Trunnion ball valves: Sealing is achieved through the pre-tightening force and the transmission of the valve stem, and the sealing performance is stable and not affected by the fluctuation of the medium pressure.
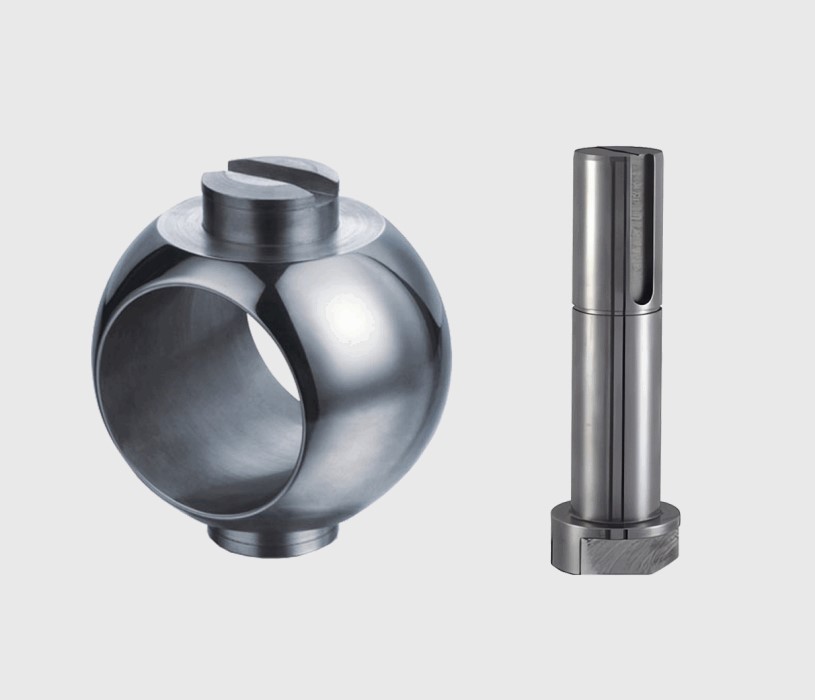
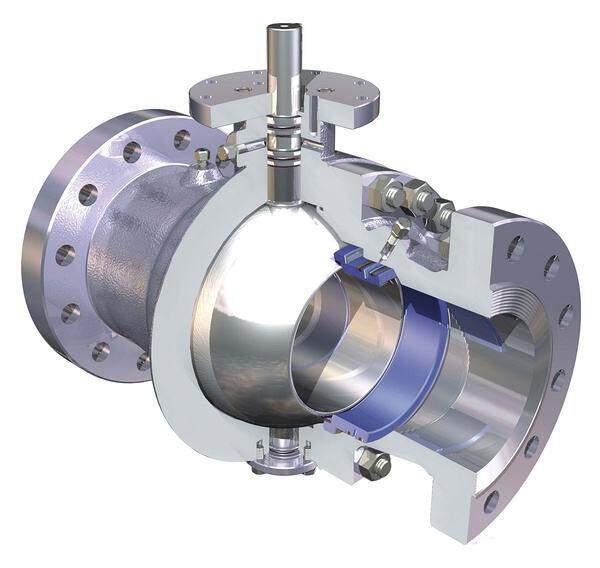
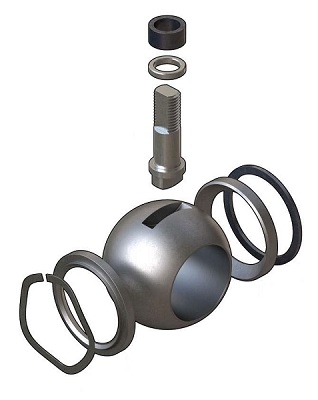
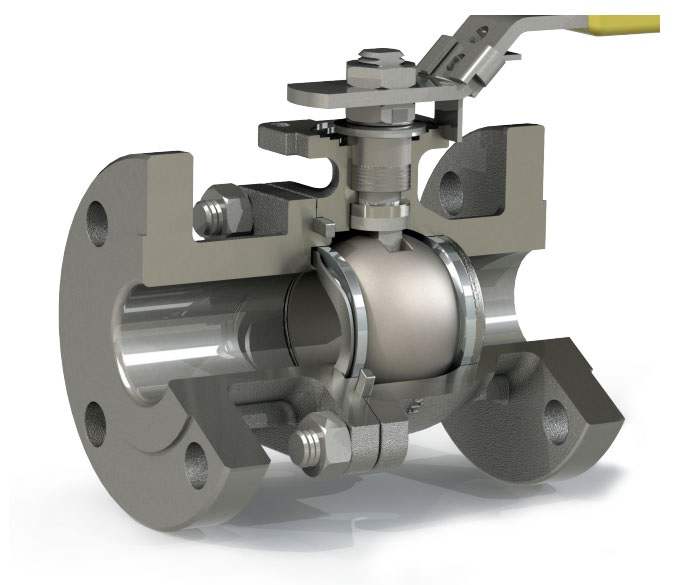
Differences in Application Scenarios.
Floating Ball Valves: They are often used in medium and low-pressure, small-diameter pipeline systems, as well as in occasions where there are high requirements for the cleanliness of the medium and the medium pressure is relatively stable, such as ordinary water supply and drainage systems, air conditioning systems, etc.
Trunnion ball valves: They are more suitable for high-pressure, large-diameter pipeline systems, as well as in occasions where there are high requirements for sealing performance and flow control, such as the key pipeline systems in industries like petrochemicals, natural gas transportation, and power.
Differences in Cost Considerations.
Floating ball valves: They are generally more cost-effective upfront. Their simpler design requires fewer components and less complex manufacturing processes, making them an attractive option for applications where budget constraints are significant.
Trunnion ball valves: Due to its more intricate design and higher – quality materials to handle high pressures, are more expensive to purchase. However, when considering the total cost of ownership over a long – term period, trunnion ball valves may prove more cost – efficient in high – pressure applications as they require less frequent maintenance and replacement.
In conclusion, the choice between floating ball valves and a trunnion ball valves depends on multiple factors, including the pressure requirements, flow characteristics, seal longevity needs, and budget constraints of a particular industrial application. By carefully evaluating these aspects, engineers and plant managers can select the valve type that best suits their operational needs.