The Energy Efficiency Revolution of Energy Efficient Industrial Pneumatic Ball Valves
Pneumatic ball valves play a important role in industrial control systems, and the improvement of their energy efficiency is of great significance for the overall energy conservation and emission reduction of the system. Thelatest technologies breakthroughs for pneumatic ball valves are:
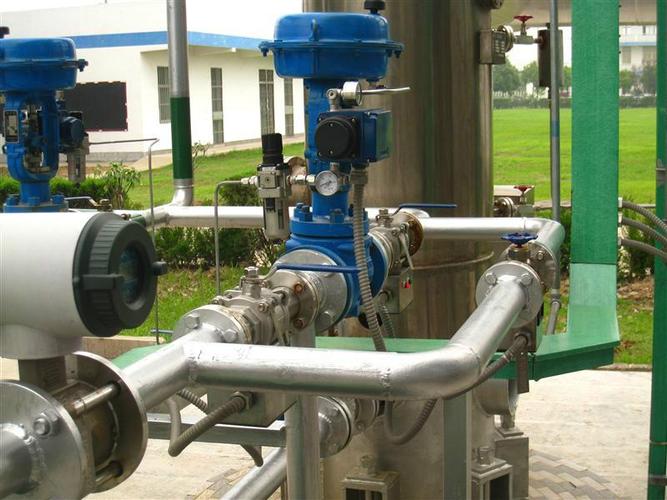
Energy efficient industrial pneumatic ball valves with smart control:
- Automated Adjustment: By introducing intelligent control algorithms, pneumatic ball valves can automatically adjust their opening degree according to real-time data, optimizing flow control and thus reducing energy waste.
- Predictive Maintenance: Utilizing sensors and big data analysis, it is possible to predict the maintenance needs of pneumatic ball valves, avoiding unnecessary shutdowns and energy consumption.
Energy saving mechanisms in industrial pneumatic ball valves:
- New Sealing Materials: The use of high-performance sealing materials, such as polytetrafluoroethylene (PTFE) and other polymer materials, improves the sealing performance, reduces leakage, and thus lowers energy losses.
- Double Sealing Structure: Designing a double sealing structure enhances the sealing effect, reduces medium leakage, and improves the energy efficiency of the system.
Optimized flow channel design:
- Fluid Dynamics Optimization: Through computational fluid dynamics (CFD) simulation, the internal flow channel design of the ball valve is optimized to reduce fluid resistance and improve fluid flow efficiency.
- Pressure Reduction and Stable Flow Technology: Integrating pressure reduction and stable flow devices inside the ball valve stabilizes the fluid pressure and flow rate, reducing energy loss.
Energy saving actuators:
- Low Power Pneumatic Actuators: Developing low power pneumatic actuators reduces the consumption of compressed air, thereby reducing energy use.
- Variable Frequency Control Technology: Adopting variable frequency control technology, the opening speed and force of the pneumatic ball valve are adjusted according to actual needs to achieve energy saving operation.
Lightweight design:
- Application of New Materials: Using lightweight and high-strength materials, such as aluminum alloy and composite materials, reduces the weight of the ball valve and lowers the energy required for driving.
- Structural Optimization: Through finite element analysis (FEA), the structure of the ball valve is optimized. On the premise of ensuring strength and sealing performance, the amount of materials used is reduced to achieve lightweight design.
Environmentally friendly surface treatment:
- Nano-Coating Technology: Adopting nano coating technology improves the wear resistance and anti-corrosion performance of the surface of the ball valve, extends its service life, and reduces resource consumption and environmental pollution.
- Green Manufacturing Process: Introducing green manufacturing processes reduces the environmental impact during the production process. For example, using powder metallurgy and precision casting technologies reduces material waste and energy consumption.