What is a Check Valve, and Its Applications.
What is a check valve?
A check valve, also known as a non-return valve or one-way valve, is an important type of valve in fluid systems. The following is a detailed introduction:
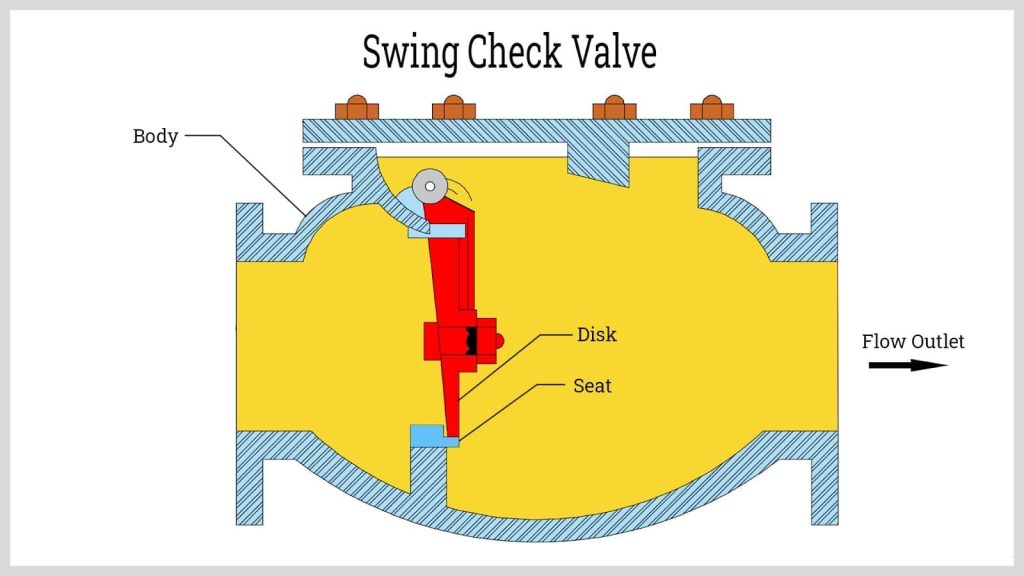
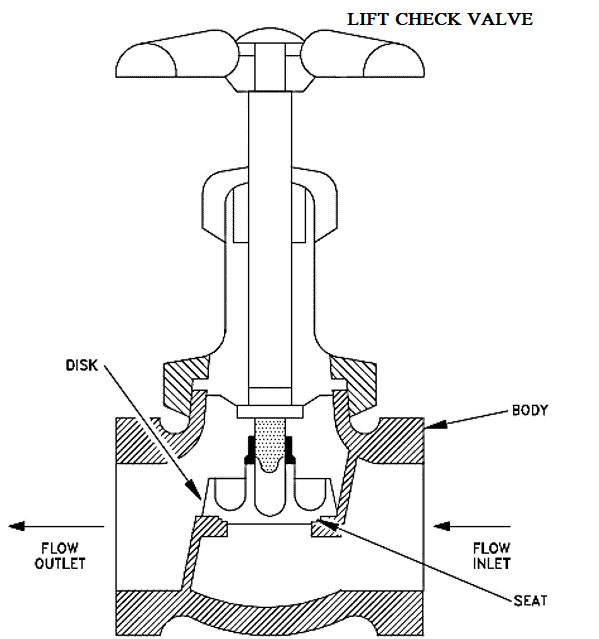
1.Structure
In terms of structure, the check valve can be devided into three types: lift check valve, swing check valve and butterfly check valve.
- Body: Similar to other valves, the body of a check valve is usually made of materials like cast iron, carbon steel, or stainless steel, providing the basic framework and fluid passage.
- Disk or Flap: This is the key moving part. It can be in the form of a disk, flap, or ball, depending on the type of check valve. For example, in a swing check valve, there is a flap that rotates around a hinge; in a ball check valve, a ball is used to control the flow.
- Seat: It provides a sealing surface for the disc or flap to rest on when the valve is closed, ensuring a tight seal to prevent backflow.
2.Working Principle
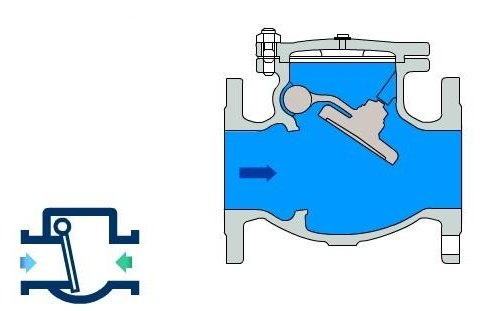
- Forward flow: When the fluid flows in the normal direction (the direction that the check valve is designed to allow), the pressure of the fluid pushes the disc or flap open. The fluid can then flow through the valve with relatively low resistance. For instance, in a lift check valve, the fluid pressure lifts the disc off the seat, allowing the fluid to pass.
- Reverse flow: When the fluid attempts to flow in the opposite direction, the pressure of the reverse flow forces the disc or flap to press against the seat. This forms a seal and blocks the flow, preventing the fluid from flowing backward. In other words, check valves work automatically based on the pressure difference of the fluid in different directions to control the flow direction.
3.Check valves have their own set of advantages and disadvantages.
Advantages
- Prevent backflow: The primary and most significant advantage of check valves is their ability to prevent backflow of fluids. They ensure that fluids flow in only one direction, protecting equipment and systems from damage that could be caused by reverse flow, such as water hammer effects or damage to pumps and compressors.
- Automatic operation: Check valves operate automatically without the need for external control or power supply. They function based on the pressure difference of the fluid, opening when the fluid is flowing in the correct direction and closing when there is a tendency for backflow. This makes them highly reliable and convenient, reducing the need for complex control systems.
- Simple structure: Most check valves have a relatively simple structure, which contributes to their reliability and ease of maintenance. With fewer moving parts compared to some other valve types, there is less likelihood of mechanical failure, and when maintenance is required, it is generally less complicated and time-consuming.
- Wide applicability: Check valves can be used with a variety of fluids, including water, oil, gas, and various chemical substances. They are suitable for different pressure and temperature ranges, depending on the materials used in their construction, making them versatile in many industrial and commercial applications.
Disadvantages
- Limited flow regulation: Check valves are primarily designed to prevent backflow and are not typically used for precise flow regulation. While they can control the direction of flow, they do not offer the same level of flow control as other valves like globe valves or control valves. In applications where accurate flow adjustment is crucial, additional flow control devices may be needed.
- Potential for leakage: Although check valves are designed to provide a tight seal to prevent backflow, they may experience leakage over time, especially if the sealing surfaces are damaged or worn. This can be a particular issue in high-pressure or high-temperature applications, where the performance of the sealing mechanism may be affected.
- Pressure drop: Check valves can cause a certain amount of pressure drop in the fluid flow path. This means that some energy is lost as the fluid passes through the valve, which may require additional pumping power to maintain the desired flow rate. In systems where energy efficiency is a critical concern, this pressure drop can be a significant drawback.
- Sensitivity to fluid properties: The performance of check valves can be affected by the properties of the fluid, such as viscosity, particulate matter, and temperature. In fluids with high viscosity or containing large amounts of particulate matter, the movement of the valve’s disc or flap may be restricted, reducing the effectiveness of the valve and potentially causing blockages.
The different applications of check valves.
There are mainly the following fields:
- Water supply and drainage systems: In water supply pipelines, check valves are used to prevent the backflow of water, ensuring that water flows in the correct direction and does not contaminate the water source. In drainage systems, they prevent sewage from flowing back into the system.
- Petroleum and chemical industries: In oil and gas pipelines, check valves are crucial for preventing the backflow of oil, gas, and various chemical fluids. This helps to maintain the stability and safety of the production process and prevent potential leakage and contamination.
- Power generation systems: In power plants, check valves are used in steam and water pipelines. For example, in the feedwater system of a boiler, check valves prevent the backflow of water, ensuring the normal operation of the boiler and the safety of the power generation equipment.
- Mechanical equipment: In many mechanical devices, such as pumps and compressors, check valves are installed at the outlet to prevent the reverse flow of fluids, protecting the equipment from damage caused by backflow and improving the reliability and service life of the equipment.