The Main Application Scenarios and Materials of Industrial Flange Gate Valves
What is Industrial Flange Gate Valves?
An industrial flange gate valve is a type of valve used to control the flow of fluids in industrial pipeline systems. It opens or closes the passage by the vertical movement of the gates. When the gate is fully raised, the fluid can pass through the valve unobstructed; when the gate descends to the lowest position, it will closely adhere to the valve seat, thereby preventing the fluid from flowing. This type of valve is typically used in applications where it requirs either fully open or fully closed, and it is not recommended for flow regulation, as this may lead to wear between the gate and the valve seat.
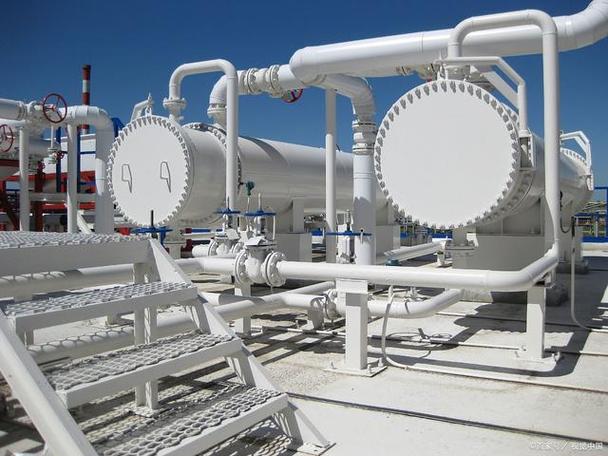
The Main Application Scenarios of Industrial Flange Gate Valves.
Industrial flange gate valves are suitable for applications in various industries.
- In the oil and gas industry, a large amount of fluids such as oil products and natural gas need to be handled. These fluids are often transported under high pressure conditions, so the valves are required to have good pressure and corrosion resistance. Gate valves can be installed on wellhead devices, gathering pipelines, and process pipelines in refineries to ensure the safe transportation of fluids.
- In the chemical industry, there is a wide variety of chemical substances with different properties. Some are highly corrosive, and some react at extremely high temperatures. For such special environments, it is particularly important to select industrial flange gate valves made of suitable materials. They can be used at the inlets and outlets of reaction kettles, at the connections of heat exchangers, and between various chemical storage tanks and transportation pipelines to ensure the safety and stability of the production process.
- In the power industry, especially in thermal power plants, steam is one of the main working media, and the pressure in the steam system is usually high. Industrial flange gate valves can effectively control the on-off of key positions of such as the main steam pipeline and the feed water pipeline, ensuring the operation efficiency of the boiler and also protecting safty of personnel.
- In industries such as metallurgy, papermaking, and pharmaceuticals, industrial flange gate valves also play an irreplaceable role. For example, in the steel manufacturing process, gate valves are needed to achieve precise control for the transportation of various gases such as oxygen and gas; the pulp transportation system in the papermaking industry also cannot do without its assistance; in order to ensure a sterile environment for drug production, pharmaceutical companies have strict requirements for the sealing performance of valves, and industrial flange gate valves become an ideal choice due to their excellent sealing performance.
Factors for Selecting Suitable Materials for Industrial Flange Gate Valves.
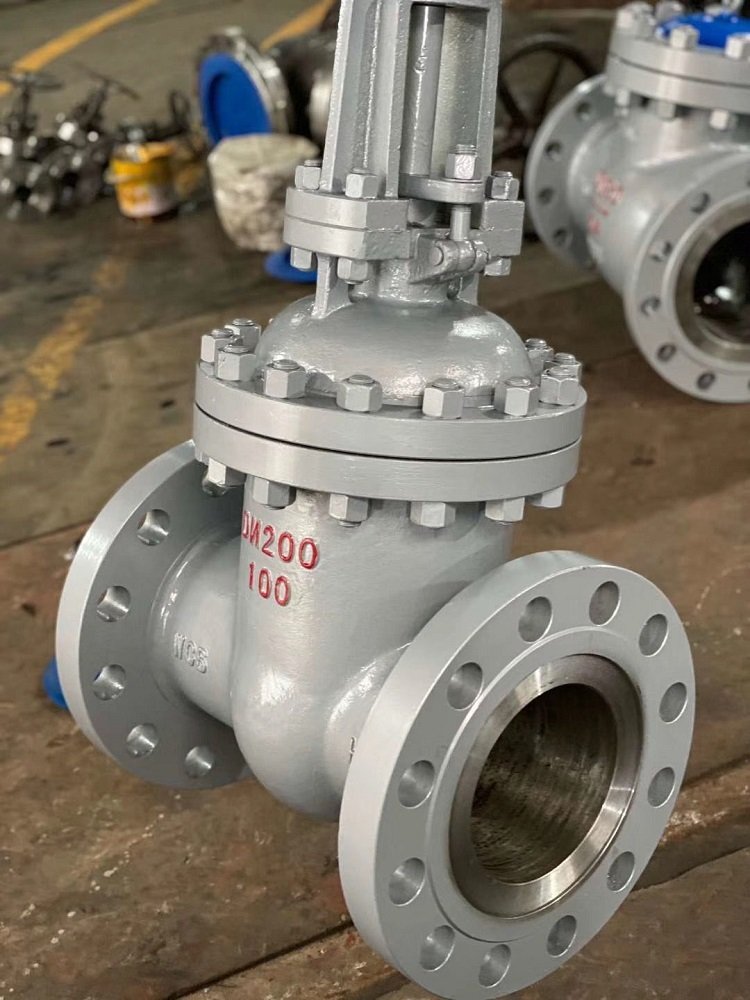
- The chemical properties of the medium are one of the important factors to determine the material selection. If the medium is corrosive, materials with good corrosion resistance must be selected. For example, for acidic or alkaline fluids, corrosion-resistant materials such as stainless steel, Hastelloy, or nickel-based alloys are usually selected. These materials perform excellently in resisting chemical erosion and can effectively extend the service life of the valve. For non-corrosive media such as water or air, carbon steel or cast iron may be sufficient.
- The working temperature range of the medium is also a factor that cannot be ignored. Different materials will have different performance characteristics at different temperatures. High temperatures may cause some metals to soften or deform, while low temperatures may lead to an increase in brittleness. Therefore, in high-temperature environments, materials with good thermal stability, such as chromium-molybdenum steel, should be selected; in low-temperature environments, low-temperature steel or austenitic stainless steel should be considered, as they can maintain good toughness and strength at extremely low temperatures.
- The pressure of the medium is also a consideration. High-pressure environments require valve materials to have high strength and good stress distribution characteristics. In this case, alloy steel may be a better choice because it can maintain structural integrity under high pressure conditions and reduce the risk of leakage caused by pressure fluctuations.
- The fluidity of the medium will also affect the material selection. If the medium contains solid particles or is prone to scaling, materials that are not easily worn and are easy to clean need to be selected. Steel materials with a hardened surface treatment or composite materials with a wear-resistant lining are good choices, as they can effectively prevent the internal components from being quickly worn and at the same time reduce the maintenance cost.
- The viscosity and phase state of the medium also need to be taken into account. High-viscosity liquids or gas-liquid mixtures may impose additional loads on the valve. In this case, valve types that are designed for easy flow and have low resistance should be prioritized, and appropriate materials should be selected to ensure smooth operation.