A Clear Idea of the Pipeline Valve.
In a pipeline system, valves are basic control components. Their main functions are to isolate equipment and the pipeline system, regulate the flow rate, prevent backflow, and regulate and discharge pressure. They can be used to control the flow of various types of fluids, such as air, water, steam, various corrosive media, slurries, oils, liquid metals, and radioactive media. Since it is very important to select the most suitable valve for the pipeline system, it has become crucial to understand the characteristics of valves and the steps and basis for selecting valves.
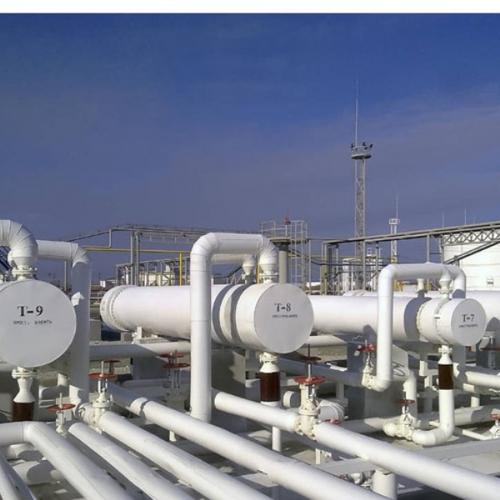
How to select the valve products?
The ultimate control of the pipeline lies in the valves. The closing and opening parts of the valve control the flow pattern of the medium within the pipeline. The shape of the flow passage inside the valve endows the valve with certain flow characteristics, and this must be taken into account when selecting the most suitable valves for pipelines.
Ⅰ.The following are the principles that should be followed when selecting valves:
Pipeline valve types are various, including gate valves, globe valves, check valves, ball valves, and butterfly valve etc., each serving specific flow control purposes.
⑴ Valves for cutting off and opening the medium.
Pipeline valves with a straight-through flow passage have relatively low flow resistance, and they are usually selected for cutting off and opening the medium. Whereas Downward-closing valves (eg. globe valves, plunger valves) have higher flow resistance than other valves due to their tortuous flow passages, so they are less frequently selected. In situations where higher flow resistance is allowed, downward-closing valves can be selected.
⑵ Valves for controlling the flow rate.
pipeline valves that are able to adjust the flow rate easily are usually selected for flow controlling. Downward-closing valves (such as globe valves) are suitable for this purpose because there is a proportional relationship between the size of their valve seats and the stroke of the closing parts. Rotary valves (plug valves, butterfly valves, ball valves) and flexure-body valves (pinch valves, diaphragm valves) can also be used for throttling control, but they are usually only applicable within a limited valve diameter range. Gate valves move the gate plate horizontally across the circular valve seat opening. They can only control the flow rate well when they are close to the closing position, so they are generally not used for flow rate control.
⑶ Valves for reversing and diverting
According to the needs of reversing and diverting, such valves can have three or more channels. Plug valves and ball valves are more suitable for this purpose. Therefore, most of the valves used for reversing and diverting are selected from one of these types of valves. However, in some cases, other types of valves, as long as two or more valves are properly connected to each other, can also be used for reversing and diverting.
⑷ Valves for media with suspended particles.
When the medium contains suspended particles, it is most suitable to use valves whose closing parts have a wiping effect when sliding along the sealing surface. If the back-and-forth movement of the closing part relative to the valve seat is vertical, then particles may be trapped. Therefore, such valves are basically only suitable for clean media unless the sealing surface material allows the embedding of particles. Ball valves and plug valves have a wiping effect on the sealing surface during the opening and closing process, so they are suitable for use in media with suspended particles.
At present, whether in the pipeline systems of the petroleum and chemical industries or other industries, the application, operation and service of valves vary greatly. To avoid even the slightest leakage, the most important and crucial element is still the valve.

Ⅱ.Pay attention to valve quality.
Valve standards standardize the requirements for various aspects such as valve design, manufacturing, inspection, and use, enabling both the manufacturing and using parties to have a common language. They can protect the respective interests of both parties from the perspective of technical regulations and provide a unified standard for evaluation.
Currently, the following problems exist in valve quality:
- Defects in valve casting.
For valve bodies made of carbon steel, especially those made of chromium-molybdenum steel, it is easy to have sand holes, burrs, and fine cracks during the casting process, and the appearance will be rough. - Valve sealing performance.
The sealing performance of a valve is an important indicator for measuring the function and quality of the valve. The problem of internal leakage of valves is serious, affectting the normal operation of the entire engineering device, and it is difficult to detect whether there is internal leakage during operation. The reasons for internal leakage of valves in most using units include that the materials of the sealing surfaces of the valve plate and valve seat do not meet the usage requirements, the machining accuracy is insufficient, the wedge angles of the valve plate and valve seat of gate valves do not match, the widths of the sealing surfaces are inconsistent, the fit is poor, the valve plate does not reach the proper position, and it cannot be completely closed. There are also cases where the packing assembly does not meet the requirements, resulting in leakage.
Ⅲ.Consider the characteristics of valves.
Generally, valves have two types of characteristics: usage characteristics and structural characteristics.
Usage Characteristics: They determine the main usage performance and application range of the valve. The usage characteristics of valves include: the type of valve (closing valve, regulating valve, safety valve, etc.); product type (gate valve, globe valve, butterfly valve, ball valve, etc.); the materials of the main valve parts (valve body, valve cover, valve stem, valve disc, sealing surface); the valve driving mode, etc.
Structural Characteristics: They determine some structural characteristics related to the installation, maintenance, and repair methods of the valve. The structural characteristics include: the structural length and overall height of the valve; the connection form with the pipeline (flange connection, threaded connection, clamp connection, external threaded connection, welded end connection, etc.); the form of the sealing surface (insert ring, threaded ring, surfacing, spray welding, valve body itself); the structural form of the valve stem (rotating stem, lifting stem), etc.
Ⅳ.The general steps for selecting pipeline valves are as follows:
- Clearly define the purpose of the valve in the pipeline system, and determine the working conditions of the valve: the applicable medium, working pressure, working temperature, etc.
- Determine the nominal diameter and connection method of the connection: flange, thread, welding, etc.
- Determine the operation mode of the valve: manual, electric, electromagnetic, pneumatic or hydraulic, electric-pneumatic linkage or electro-hydraulic linkage, etc.
- Based on the medium transported by the pipeline, working pressure, and working temperature, determine the materials of the valve housing and internal parts: gray cast iron, malleable cast iron, ductile iron, carbon steel, alloy steel, stainless acid-resistant steel, copper alloy, etc.
- Select the type of valve: closing valve, regulating valve, safety valve, etc.
- Determine the type of valve: gate valve, globe valve, ball valve, butterfly valve, throttle valve, safety valve, pressure reducing valve, steam trap, etc.
- Determine the parameters of the valve: for automatic valves, first determine the allowable flow resistance, discharge capacity, back pressure, etc. according to different needs, and then determine the nominal diameter of the pipeline and the diameter of the valve seat hole.
- Determine the geometric parameters of the selected valve: structural length, flange connection form and dimensions, the height dimension of the valve in the vertical direction after opening and closing, the dimensions and quantity of the connecting bolt holes, the overall external dimensions of the valve, etc.
- Utilize existing materials: valve product catalogs, valve product samples, etc. to select appropriate valve products.
So far, the valve industry has been able to produce a complete range of 12 categories of valve products, including gate valves, globe valves, throttle valves, plug valves, ball valves, electric valves, diaphragm valves, check valves, safety valves, pressure reducing valves, steam traps, and emergency shut-off valves, with more than 3,000 models and more than 4,000 specifications. The highest working pressure is 600MPa; the largest nominal diameter reaches 5350mm; the highest working temperature is 1200°C; the lowest working temperature is -196°C, and the applicable media include water, steam, oils, natural gas, highly corrosive media (such as concentrated nitric acid, medium-concentration sulfuric acid, etc.), flammable media (such as benzene, ethylene, etc.), toxic media (such as hydrogen sulfide), explosive media, and radioactive media (sodium metal, primary loop pure water, etc.). The materials of valve pressure-bearing parts include brass, cast iron, ductile iron, high-silicon cast iron, cast steel, forged steel, high/low alloy steel, stainless steel 304, stainless acid-resistant steel, duplex stainless steel, titanium alloy, etc., and various electric, pneumatic, manual, and hydraulic valve driving devices can be produced.
Facing such a large variety of valves and such complex working conditions, to select the most suitable valves for pipelines, one should first understand the characteristics of the valve; secondly, master the steps for selecting the valve; and thirdly, follow the principles for selecting the valve.