Classification of Globe Valves
Classification by Channel Direction
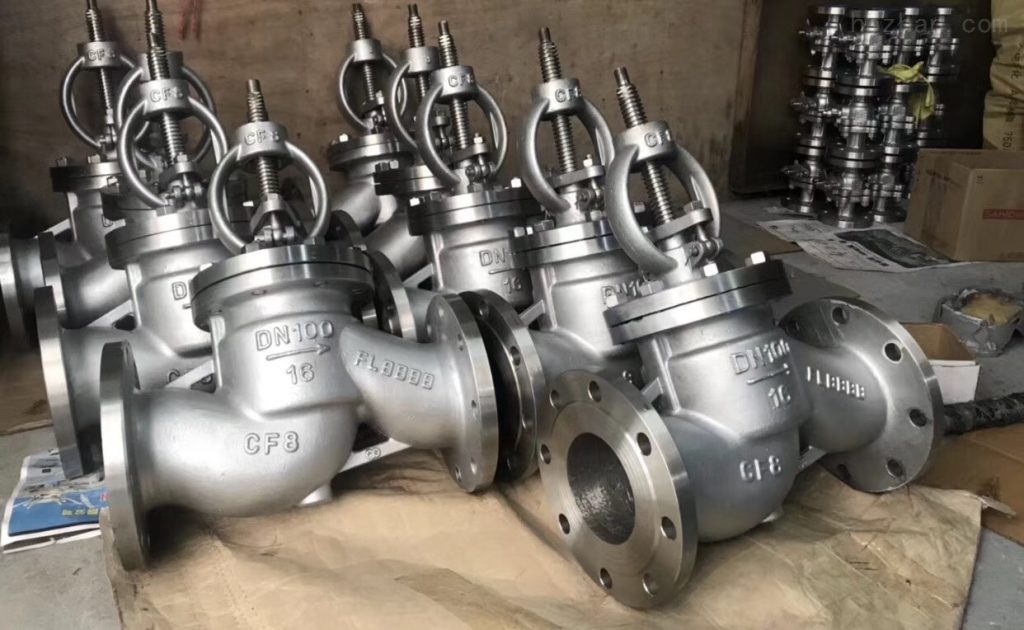
Straight-through Globe Valve
The inlet and outlet channels of the medium are in the same direction, forming an angle of 180°. The degree of destruction of the flow state is relatively small, and the pressure loss through the valve is relatively small.
Direct-current Globe Valve
The valve stem and the channel form a certain angle, and the sealing surface of the valve seat and the inlet and outlet channels also have a certain angle. The fluid hardly changes its flow direction, and it has the smallest flow resistance among globe valves. It is suitable for pipelines with coking and solid particles.
Angle Globe Valve
The inlet and outlet channels of the medium are not in the same direction, forming an angle of 90°. A certain pressure drop will be generated. Its greatest advantage is that it can be installed at the bend of the pipeline system, which not only saves elbow fittings but also facilitates operation.
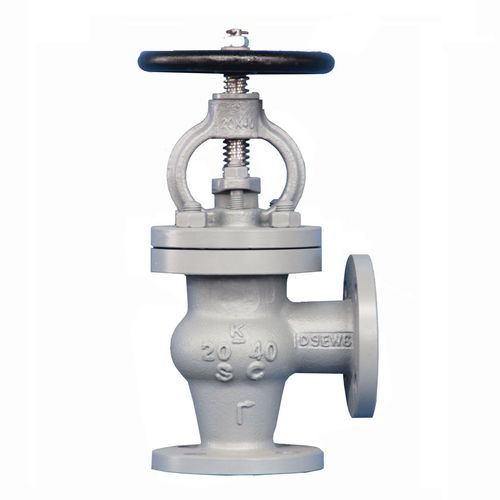
Classification by the Position of the Thread on the Screw
Rising Stem Globe Valve
The thread of the valve stem is outside the housing and does not come into direct contact with the working medium. The thread of the valve stem is not corroded by the medium, which is convenient for lubrication and makes the operation labor-saving.
Non-rising Stem Globe Valve
The thread of the valve stem is inside the valve body and comes into direct contact with the working medium. The thread of the valve stem is prone to be corroded by the medium, and it cannot be lubricated. It is mostly used in occasions where the nominal diameter is small and the working temperature of the medium is not high.
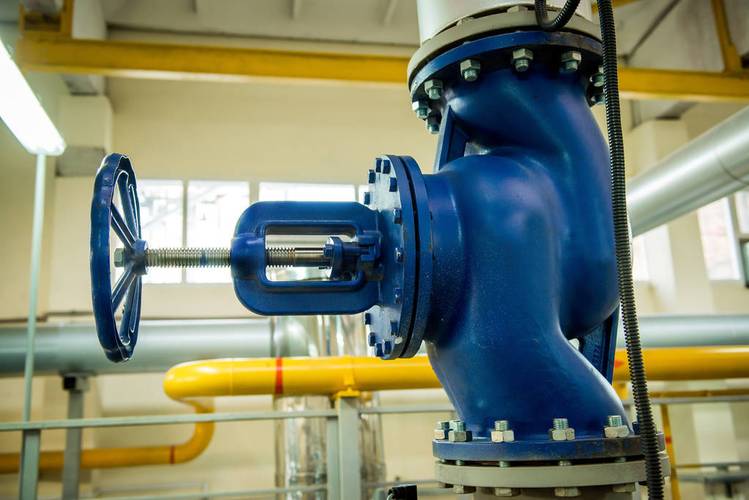
Classification by Purpose
Fluorine-lined Globe Valve
Fluorine-lined valves, also known as fluoroplastic-lined corrosion-resistant valves, are made by placing polytetrafluoroethylene resin (or processed profiles) on the inner wall of the pressure-bearing parts of steel or iron valves (the same method is applicable to the inner lining of various pressure vessels and pipeline accessories) or the outer surface of the valve internals through the method of molding (or inlaying). Various valves and pressure vessels are made by taking advantage of its unique performance in resisting strong corrosive media.
The fluorine-lined globe valve is suitable for use on pipelines with various concentrations of aqua regia, sulfuric acid, hydrochloric acid, hydrofluoric acid, and various organic acids, strong acids, and strong oxidants at a temperature range of -50 to 150°C. It is also suitable for use on pipelines with various concentrations of strong alkali organic solvents and other corrosive gas and liquid media.
National Standard Globe Valve
The national standard globe valve is the most commonly used product in the globe valve series. The API American standard globe valve complies with ANSI and API standards. The sealing surfaces of the valve disc and the valve seat are surfacing welded with Stellite cobalt-based hard alloy of different hardnesses. It has reliable sealing, high hardness, wear resistance, high-temperature resistance, corrosion resistance, good anti-scuffing performance, and a long service life.
Needle Valve
The needle valve is a small-bore instrument valve that plays the role of opening and closing and precise flow control in the instrument measurement pipeline system. It mainly includes the power station instrument series, the special oilfield series, the American standard series, etc.
Cryogenic Globe Valve
The cryogenic globe valve usually refers to a valve with a working temperature lower than -110°C, and it is widely used in the liquefied natural gas, liquefied petroleum gas, and other cryogenic industries.
Currently, globe valves applicable to a temperature of -196°C can be manufactured. All parts are pre-treated at a low temperature with liquid nitrogen, completely avoiding sealing deformation and leakage during the use process.
Plunger Globe Valve
The plunger valve, also known as the plunger stop valve, has a radial sealing structure for its sealing surface. Two elastic sealing rings sleeved on the polished plunger are tightened by the load applied to the valve cover by the connecting bolts between the valve body and the valve cover to achieve the sealing of the stop valve.
Insulated Jacketed Globe Valve
The insulated jacketed globe valve adopts an insulated jacket design. External heat sources are used for circulating heating outside the valve, which can effectively prevent the temperature loss of the medium when it passes through the valve and ensure the temperature of the medium.
Oxygen-specific Globe Valve
The oxygen-specific globe valve is cast from high-quality silicon brass or stainless steel, and it has the advantages of high mechanical strength, wear resistance, good safety, etc.
It is used on oxygen pipelines and has the best explosion-proof and flame-retardant performance, eliminating the unsafe factors on the oxygen pipelines. It is widely used in the pipe networks of oxygen-using projects such as steel, metallurgy, petrochemical, and chemical industries. In addition to having the functions of ordinary valves, it also has its own characteristics.
During the manufacturing process, strict oil-free measures are adopted, and all parts are strictly degreased before installation.
Bellows Globe Valve
The bellows globe valve adopts a formed stainless steel bellows design. The bellows can withstand 10,000 reciprocating tests without failure, and it has reliable sealing performance. It is suitable for industrial and mining environments with flammable, explosive, toxic, and harmful media, and can effectively prevent the external leakage of the valve.