Globe Valve VS Diaphragm Valve: Advantages and Disadvantates.
A globe valve refers to a valve in which the closing part (valve disc) moves along the center line of the valve seat. According to this movement form of the valve disc, the change in the opening of the valve seat is in a direct proportional relationship with the stroke of the valve disc. Since the opening or closing stroke of the valve stem of a globe valve is relatively short, and it has a very reliable shut-off function, and also because the change in the opening of the valve seat is in a direct proportional relationship with the stroke of the valve disc, it is very suitable for flow regulation. Therefore, globe valves are very suitable for use as a shut-off, regulating, or throttling valve.
Advantages and disadvantages of globe valves.
Advantages:
- During the opening and closing process, the friction force between the valve disc and the sealing surface of the valve body is smaller than that of a gate valve, so it is more wear-resistant.
- The opening height is generally only about 1/4 of the passage of the valve seat, which is much smaller than that of a gate valve.
- Usually, there is only one sealing surface on both the valve body and the valve disc, so the manufacturing process is relatively simple, and it is convenient for maintenance.
- Since its packing is generally a mixture of asbestos and graphite, the temperature resistance grade is relatively high. Generally, globe valves are used for steam valves.
Disadvantages:
- Since the flow direction of the medium through the valve changes, the minimum flow resistance of a globe valve is also higher than that of most other types of valves.
- Due to the relatively long stroke, the opening speed is slower than that of a ball valve.
What is a diaphragm valve?
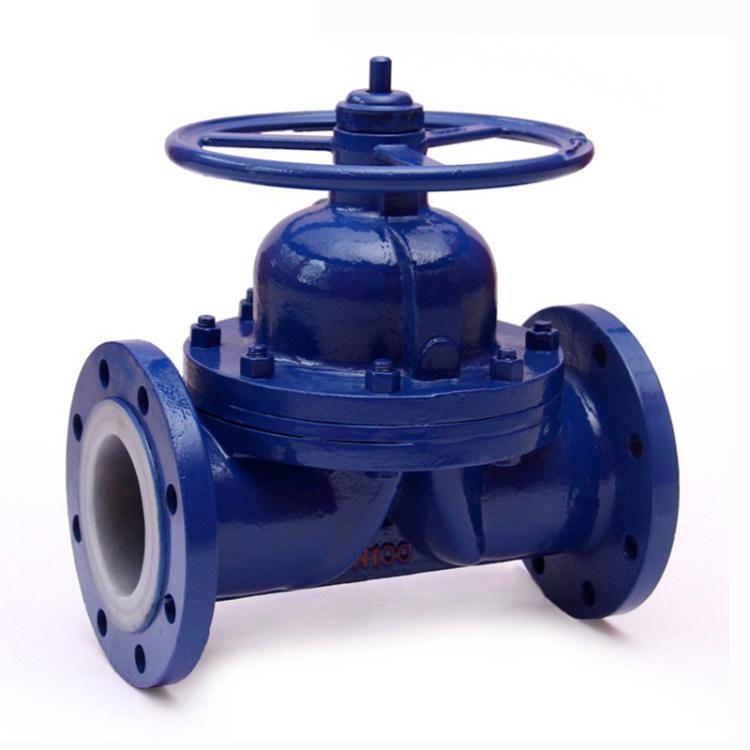
What are the advantages and disadvantages of diaphragm valves?
A diaphragm valve refers to a valve in which a flexible membrane or a combined diaphragm is installed inside the valve body and the valve cover, and its closing part is a compression device connected to the diaphragm. The valve seat can be in the shape of a weir or the wall of a straight through flow passage.
Advantages:
- The operating mechanism is separated from the medium passage, which not only ensures the purity of the working medium but also prevents the possibility of the medium in the pipeline impacting the working components of the operating mechanism. There is no need to use any form of separate seal at the valve stem, unless it is used as a safety device when controlling harmful media.
- Since the working medium only comes into contact with the diaphragm and the valve body, and both can be made of a variety of different materials, this valve can ideally control a variety of working media, especially suitable for media with chemical corrosion or suspended particles.
- The structure is simple, consisting of only three components: the valve body, the diaphragm, and the valve cover assembly. This valve is easy to disassemble and repair quickly, and the diaphragm can be replaced on-site and within a short period of time.
Disadvantages:
- Due to the limitations of the lining process of the valve body and the manufacturing process of the diaphragm, it is very difficult to manufacture a large valve body lining and a large diaphragm. Therefore, the diaphragm is not suitable for use in large-diameter pipes, and it is generally applied to pipelines with a DN ≤ 200mm.
- Due to the limitations of the diaphragm material, the diaphragm valve is suitable for low-pressure and low-temperature occasions. Generally, the temperature does not exceed 180°C.
- The regulating performance is relatively poor, and it can only be adjusted within a small range (generally, when it is closed to 2/3 of the opening degree, it can be used for flow regulation).