Floating Ball Valve

The floating ball valve has many advantages in industrial applications.
Firstly, its pressure resistance performance is particularly outstanding. Thanks to its excellent sealing design, it can easily withstand high-pressure environments and ensure no leakage. Thus it is applicable to high-pressure industries such as chemical engineering and petroleum.
Secondly, the floating ball valve has a long service life. The valve body is made of sturdy and corrosion-resistant materials, such as cast steel and stainless steel. Moreover, with a simple internal structure, it has a low failure rate, significantly reducing the maintenance cost.
Thirdly, it enables precise and stable flow control. The small-diameter design, combined with a reasonable internal structure, allows the medium to flow smoothly without jetting or fluctuations.
Finally, easy operation is also a major highlight of the floating ball valve. It supports multiple control methods, including manual, pneumatic, and electric control, and is adaptable to various operating scenarios. It is especially suitable for remote control in high-position or hazardous areas, providing both safety and flexibility.
Ball float valve.
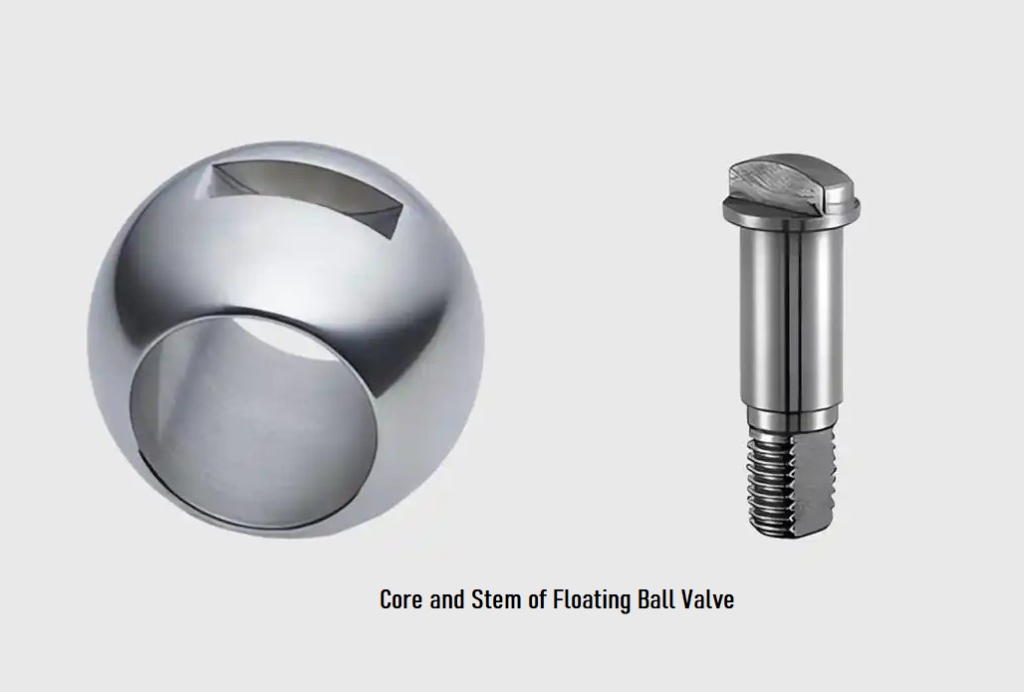
The floating ball valve clamps the intermediate ball core between the two seat seals at the inlet and outlet. By rotating the valve stem, the ball core is driven to rotate 90°, thus achieving the opening and closing actions of the ball valve. When the ball core is closed, the semi-circular shape at the top of the valve stem is in the same direction as the semi-circular groove of the ball core. Because the ball core moves towards the outlet direction under the act of the medium pressure, it is called a floating ball valve.
The inlet and outlet valve seats have a certain sealing pre-tightening force and wrap the ball core. When the valve is closed, the medium pressure pushes the ball core, making it press tightly against the outlet valve seat seal, which enhances the sealing performance of the outlet valve seat and thus ensures the sealing performance of the ball valve.
Features of Topwells floating ball valve:
- It has the function of indicating a switch. The ball, stem, and handle are the moving parts of the floating ball valve. Our design changes the top of the stem into a flat square structure, This provides a clear indication of the valve in the open position during service when the handle is parallel to the line; When the handle is perpendicular to the line, indicates that the valve is closed;
- It is equipped with a locking device. Topwells adds two limit screws in the packing gland and coordinates the switch locating tab with a lock hole to prevent the damage to the valve caused by excessive opening, On the other hand, it is guaranteed that the valve can be locked in the fully open or fully closed state and cannot be operated wrongly by any personnel ;
- With the valve stem blow out proof structure.Topwells set a convex platform at the bottom of the stem structure, on one hand, to ensure the stem will not be blew out of the body, on the other hand, to prevent even packing damage. The valve stem convex sets and close contact between the body and stem will avoid a medium-large leaking out;
- It is equipped with the anti-static device. Friction between the ball, PTFE, and other non-metallic materials will generate electrostatic accumulation on the ball. To prevent the danger of electrostatic spark caused by the working condition, Topwells set up an anti-static device at the valve stem, which can export the static electricity through the valve stem.
Technical Specifications
Design | API 6D, API 6DSS, ASME B16.34, ISO 14313, ISO 17292 |
Design Pressure | ASME B16.34, EN 1092-1, ISO 17292 |
Body Wall Thickness | ASME B16.34, ASME VIII Div. I, ISO 17292 |
Face to Face | API 6D, ASME B16.10 Long pattern |
Temperature Range | -50° to 200°C (-58° to 392°F) |
Pressures Range | PN10 (ANSI 150) to PN420 (ANSI 2500) |
Size Range | DN15 (1/2″) to DN250 (10″) |
End connections | ASME B16.5 Flanged RF, FF, RTJ ASME B16.25 Butt-Weld BW ASME B16.11 Socket-Weld SW ASME B36.10 Plain-End PE ASME B1.20.1 Threaded NPT (F/M) |
Main Part Material
No | Part | Material |
1 | Body | ASTM A216 WCB |
2 | Bonnet | ASTM A216 WCB |
3 | Ball | ASTM A105 |
4 | Seat | ASTM A105 + PTFE |
5 | Stem | ASTM A182 F6a |
6 | Anti-static Device | SS304 |
7 | Gasket | Graphite + SS304 |
8 | Bolt | ASTM A193 B7 |
9 | Nut | ASTM A194 2H |
10 | O-ring | Viton A |
11 | Lever | ASTM A216 WCB |
The data is for reference only, please consult sales@wayvalve.com for details.
The float ball valve is mainly applied in the following fields.
- Emergency shut-off systems.
Pipeline systems involved in fuels, water, or critical gases often require a fast-responding shut-off valve in case of emergencies. A floating ball valve works fast and is therefore suitable for SIL 3 emergency shut-offs. - Water systems.
Water distribution systems require that pressure is maintained at optimum levels to sustain flow and prevent air pockets from restricting the flow of water. The flow of water also needs to be controlled to prevent overflows. A floating ball valve would be a good choice for water system control as it is pressure-sensitive and can open and shut as needed based on pressure conditions. - Pipeline pressure relief.
Pipeline pressure management is essential to avoid busts and similar accidents. A floating ball valve can be added in a pipeline as a pressure outlet valve as it takes on the pressure while remaining intact as opposed to a mounted ball valve that could sometimes blow out.
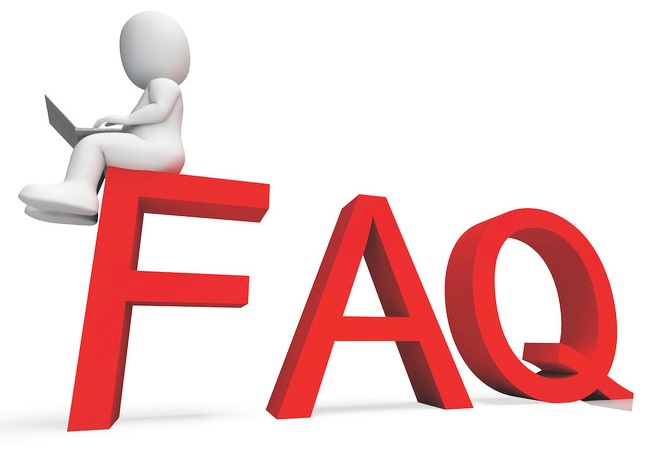
What is the difference between a ball valve and a floating ball valve?
A ball valve is a general type of valve that uses a ball with a hole to control fluid flow. A floating ball valve is a specific kind of ball valve. In a floating ball valve, the ball is free-floating and is sealed against the seat by the fluid pressure. In contrast, some other ball valves may have a fixed-position ball. So, the main difference lies in the way the ball is supported and sealed.
Are floating ball valves bidirectional?
Yes, floating ball valves are generally bidirectional. The floating ball design allows for sealing in both directions, enabling fluid flow to be controlled regardless of the flow direction.
INQUIRY