Electric Gate Valve
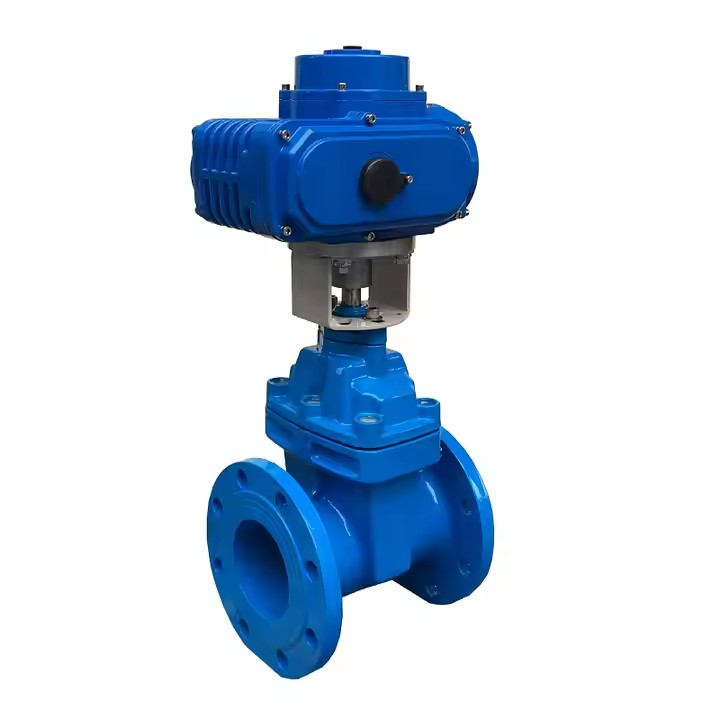
Electric gate valves are key components in the field of industrial automation. Based on their characteristics, they can be divided into two major categories: angular-stroke electric gate valves and linear motion electric gate valves.
Electric gate valves are widely used to regulate the flow of media in pipelines for liquids, gases, and air systems. Usually driven by motors, their opening and closing actions need time for simulation, making them suitable for regulation work. These valves can withstand voltage shocks and are applicable to various working environments. In contrast, solenoid valves open and close rapidly but are generally used for small- flow, low-pressure, and high -frequency switching scenarios. Electric gate valves can precisely control the flow of media with adjustable openings from fully open to fully closed, or half-open, which solenoid valves can’t achieve.
Main features of electric gate valves.
- The electric gate valve can be operated remotely and the user can operate and check the valve status in the control room. It reduces the waste of personnel needed to run to the site to close gate valves without electric actuators and also reduces the situation that valves cannot be closed in dangerous situations;
- The electric gate valve can be customized asbestos-free packing or graphite packing;
- The electric gate valve will fix the electric actuator in the transportation process to prevent the damage to the electric actuator caused by the bump in the transportation process;
- Low torque of WayValve electric gate valve can reduce the cost of the electric actuator.
Material Standard
No | Part | Material |
1 | Body | ASTM A351 CF8 |
2 | Seat Ring | ASTM A182 F304 + 13Cr |
3 | Wedge | ASTM A351 CF8 + 13Cr |
4 | Stem | ASTM A182 304 |
5 | Bonnet Gasket | Graphite + SS304 |
6 | Bonnet Bolt | ASTM A193 B8 |
7 | Bonnet Nut | ASTM A194 8 |
8 | Bonnet | ASTM A351 CF8 |
9 | Backseat | ASTM A182 304 |
10 | Stem Packing | Reinforced Graphite |
11 | Motorized Actuator | ASTM A351 CF8 |
The data is for reference only, please consult sales@wayvalve.com for details.
Applications of the electric gate valve.
Electric gate valves are widely used in multiple fields, mainly including petrochemical, metallurgy, electric power, food, pharmaceutical, and municipal sectors, etc.
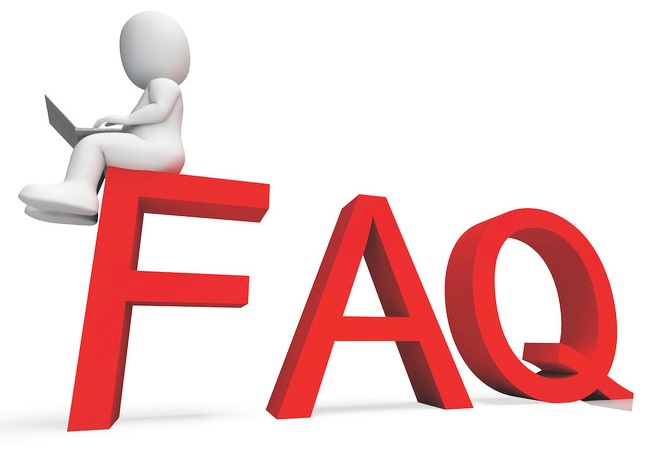
Can gate valves be automated?
Yes, gate valves can be automated. Automation of gate valves is achieved by integrating them with electric, pneumatic, or hydraulic actuators.
An electric actuator, for example, receives an electrical control signal. Once it gets the signal, it converts electrical energy into mechanical energy, which drives the valve stem to move the gate, thus opening or closing the valve.
Automated gate valves offer several advantages. They can be remotely controlled, allowing for easy operation in hard-to-reach or dangerous areas. In industrial processes, they enable precise and timely flow control, improving efficiency and safety. Moreover, they can be integrated into automated control systems for real-time monitoring and adjustment, which is crucial in industries like petrochemicals, power generation, and water treatment.
Can electric gate valves be used in hazardous environments?
Yes, electric actuated gate valves can be used in hazardous environments, but specific precautions and designs are necessary to ensure safety. Here’s a detailed explanation:
Key Considerations for Hazardous Environments.
1, In environments with flammable gases, vapors, or dust (e.g., oil refineries, chemical plants), valves must comply with explosion-proof standards (e.g., ATEX, UL Class I Div. 1). Electric actuators may be enclosed in explosion-proof housings that contain any internal sparks or heat, preventing ignition of surrounding hazardous materials.
2, Valve bodies and components may use corrosion-resistant materials (e.g., stainless steel, hastelloy) to withstand aggressive chemicals or harsh atmospheres. Seals and gaskets are often made from specialized materials (e.g., PTFE, viton) to prevent leaks and maintain integrity in corrosive conditions.2
3, IP (Ingress Protection) ratings (e.g., IP66, IP68) ensure resistance to water, dust, and high-pressure jets, suitable for wet or dusty hazardous areas.
4, Temperature-resistant designs may be needed for high-temperature environments (e.g., furnace applications) to prevent component degradation.
Intrinsically safe (IS) actuators limit electrical energy to levels that cannot ignite hazardous substances, often used in zones with high explosion risks.
Electrical components may include spark-proof connections and insulated wiring to minimize the risk of electrical arcs.
Limitations and Mitigation.
1, Electrical failures in hazardous areas can be critical. Backup power systems (e.g., UPS) or fail-safe actuators (e.g., spring-return designs) are often installed to maintain valve position during outages.
2, Regular inspection of explosion-proof enclosures and seals is essential to prevent degradation that could compromise safety.
Electric gate valves are suitable for hazardous environments when designed and certified for such conditions. Compliance with industry standards, proper material selection, and safety features are crucial to mitigate risks and ensure reliable operation. Always consult manufacturer specifications and local safety regulations when deploying valves in hazardous areas.
INQUIRY