What is a Throttle Valve and a Relief Valve?
I. Throttle Valve
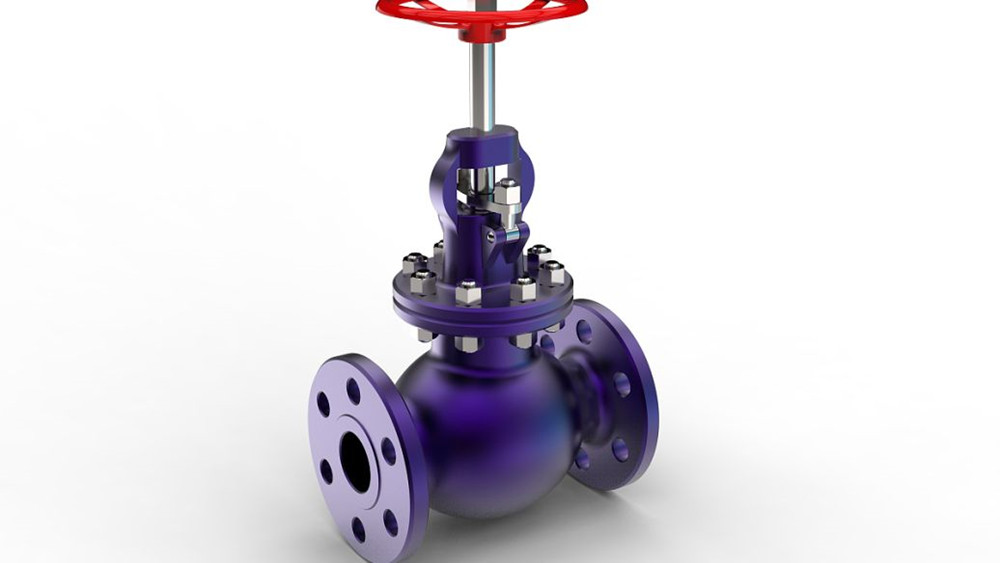
- (1) A throttle valve is a valve that controls the fluid flow rate by changing the throttling cross-section or the throttling length. When a throttle valve and a check valve are connected in parallel, a one-way throttle valve can be formed. Throttle valves and one-way throttle valves are simple flow control valves. In a fixed-displacement pump hydraulic system, in combination with a relief valve, a throttle valve can form three types of throttle speed control systems, namely, the inlet circuit throttle speed control system, the return circuit throttle speed control system, and the bypass throttle speed control system.
- (2) The throttle valve does not have a flow negative feedback function and cannot compensate for the speed instability caused by changes in the load. It is generally only used in occasions where the load change is not large or the requirement for speed stability is not high. It is a type of hydraulic pressure control valve that mainly plays the roles of constant pressure overflow and safety protection in hydraulic equipment.
- (3) The performance requirements for a throttle valve are as follows: 1. It should have a large flow adjustment range, and the change in the flow pressure difference should be smooth; the internal leakage amount should be small, and if there is an external leakage oil port, the external leakage amount should also be small; the adjustment torque should be small, and the action should be sensitive.
II. Relief Valve
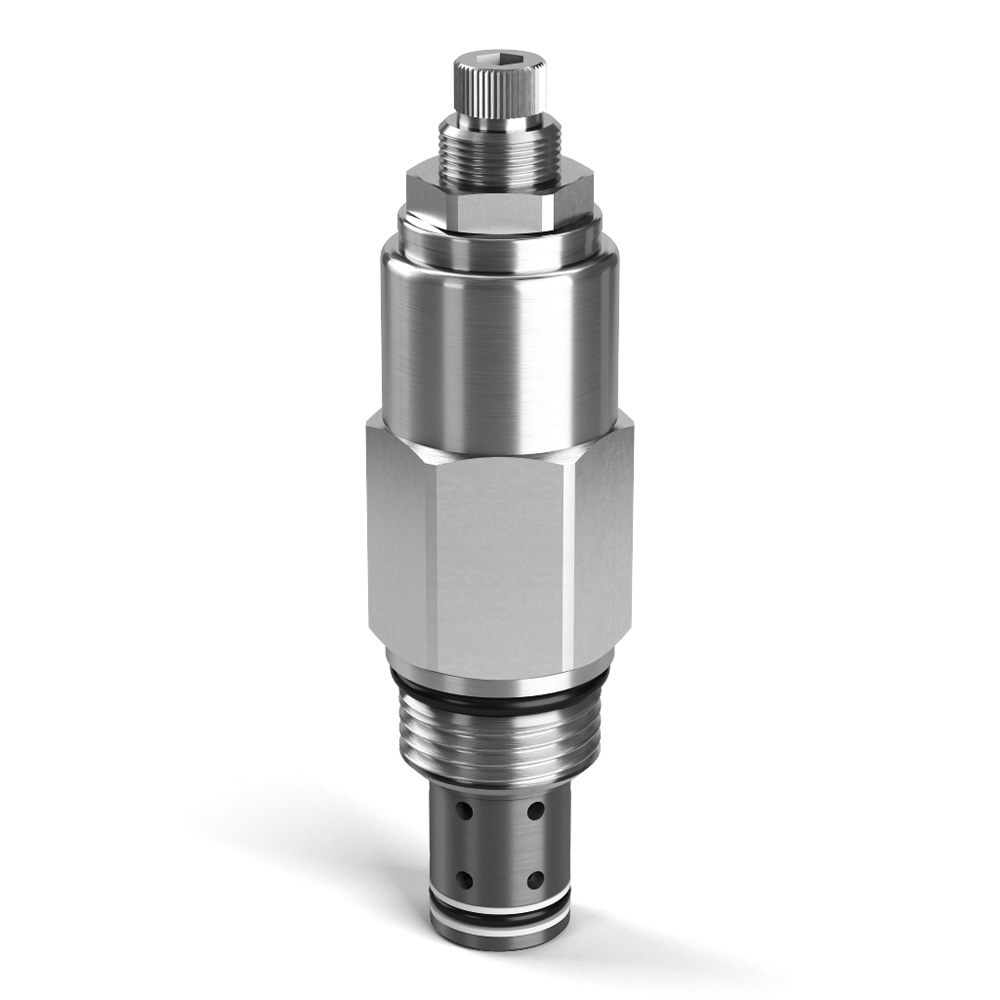
- (1) The function of constant pressure overflow of the relief valve: In a fixed-displacement pump throttle control system, the hydraulic oil pump provides a constant flow rate. When the system pressure increases, the flow demand will decrease. At this time, the relief valve opens, allowing the excess flow to return to the oil tank, ensuring that the pressure at the inlet of the relief valve, that is, the pressure at the outlet of the pump, remains constant (the valve port often opens with pressure fluctuations).
- (2) The function of safety protection: When the system is operating normally, the valve is closed. It only opens for overflow when the load exceeds the specified limit (the system pressure exceeds the set pressure) to provide overload protection, preventing the system pressure from increasing further (usually, the set pressure of the relief valve is 10% – 20% higher than the maximum working pressure of the system).
- (3) In practical applications, it is generally used as follows: as an unloading valve, as a remote pressure regulating valve, as a multi-stage high-low pressure control valve, as a sequence valve, and for generating back pressure (connected in series in the return oil circuit). Generally, there are two structures for relief valves: 1. Direct-acting relief valve. 2. Pilot-operated relief valve.