Differences Between a Regenerative Turbine Pump and a Centrifugal Pump
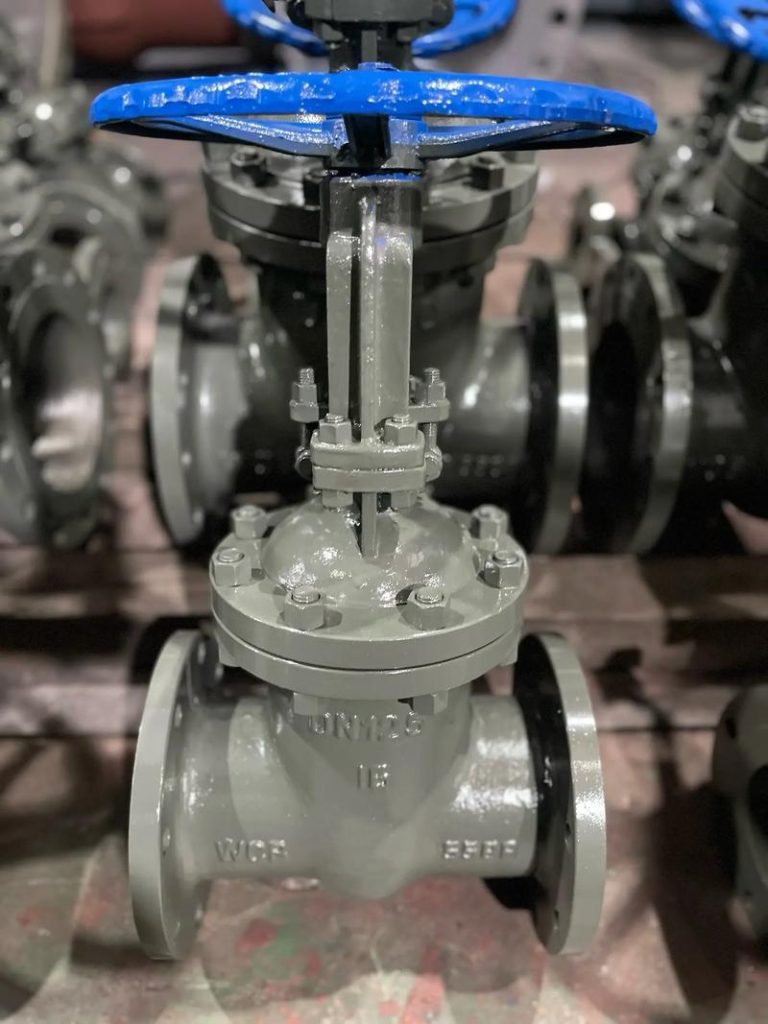
What is a Regenerative Turbine Pump?
For Handling Liquid, regenerative turbine pumps fill a need between centrifugal and positive displacement designs. They combine high discharge pressure of displacement types with the flexible operation of centrifugals. They are a low-capacity high-head type used on heads up to 5400 ft (1645 m) and in capacities up to 150 gpm (34 m3/hr). Regenerative turbine pumps are known by several names, such as vortex, peripheral and regenerative. None of these give a true description of the pump, but regenerative turbine is the nearest. Several types of rotating pumps have been called “turbine”. Among them are the horizontal-shaft diffuser type and vertical-shaft deep-well centrifugal. The operation of the small pump with a big head, the regenerative turbine pump, is discussed here.
Regenerative Turbine Pump Design
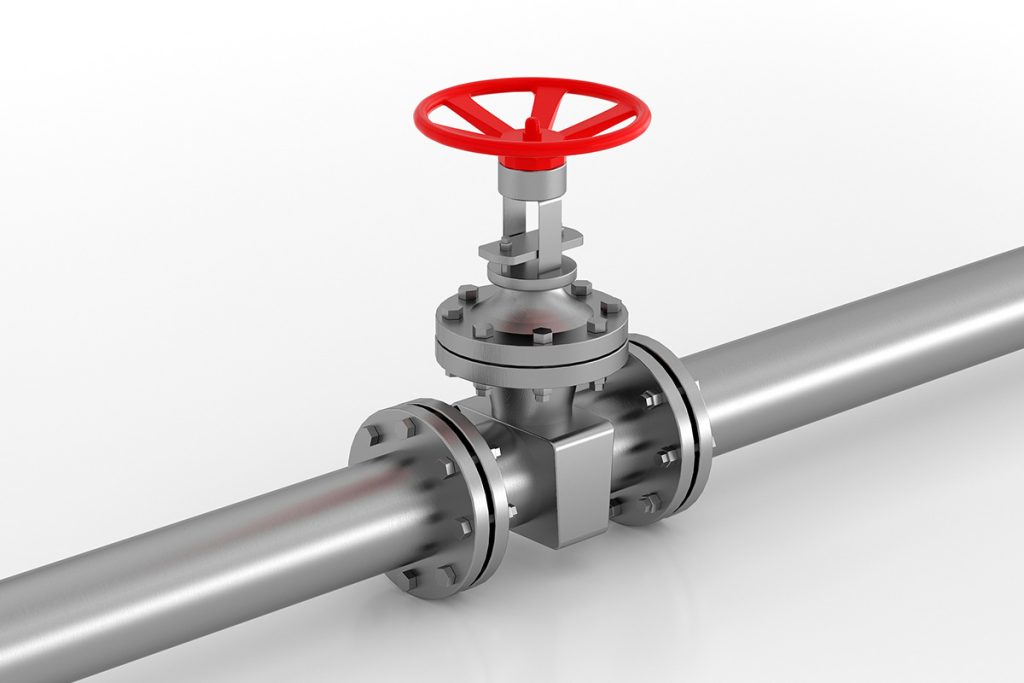
It show cross sections through a regenerative turbine pump. It shows the general construction to be quite like many small centrifugal designs. Its shaft, often made of stainless steel, is supported by two ball bearings. The impeller is overhung, a common construction for centrifugal pumps. The pump is generally supplied with a mechanical seal as standard. The chief difference between centrifugal and regenerative turbine pumps is in the impeller. In the regenerative turbine pump a double row of vanes is cut in the impeller’s rim. These vanes rotate in a channel, Liquid flows in at the suction and is picked up by the impeller’s vanes.
After making nearly one revolution in the annular channel, the fluid has a high velocity that sends it out the discharge. Liquid entering a centrifugal pump’s impeller can pass between its vanes but once. It has energy added to it only while going from the impeller’s eye to its rim. In a regenerative turbine pump, liquid recirculates between the impeller’s vanes. Because of this action the fluid flows in a path like a screw thread (helical) as it is carried forward. Consequently, energy is added to the fluid in a regenerative motion by the impeller’s vanes as it travels from suction to discharge. This regenerative action has the same effect as multistaging in a centrifugal pump. In a multistage centrifugal, the fluid’s pressure is the result of energy added in the different stages. In the same way, in a regenerative turbine pump, pressure at its discharge is the result of energy added to the fluid by a number of impeller vanes.
How does a Regenerative Turbine pump work?
The primary difference between a centrifugal and a regenerative turbine pump is that fluid only travels through a centrifugal impeller once, while in a turbine, it takes many trips through the vanes. Referring to the cross-section diagram, the impeller vanes move within the flow-through area of the water channel passageway. Once the liquid enters the pump, it is directed into the vanes, which push the fluid forward and impart a centrifugal force outward to the impeller periphery. An orderly circulatory flow is therefore imposed by the impeller vane, which creates fluid velocity. Fluid velocity (or kinetic energy) is then available for conversion to flow and pressure depending on the external system’s flow resistance as diagrammed by a system curve.
It is useful to note at this point, that in order to prevent the internal loss of the pressure building capability of an MTH regenerative turbine, close internal clearances are required. In many cases, depending on the size of the pump, impeller to casing clearances may