Socket Weld VS Butt Weld
Among the pipeline connection methods, socket weld(abbreviated as SW) and butt weld(abbreviated as BW) are two common connection methods by welding. Socket welding or butt welding each has its own characteristics and suitable for different scenarios.
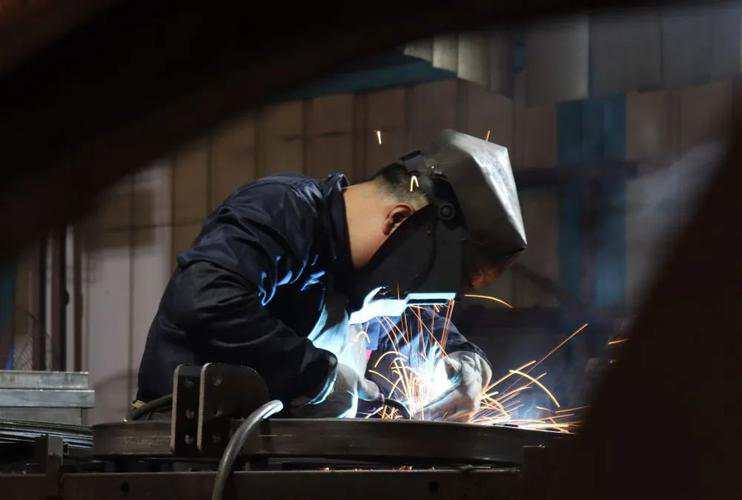
What is socket welding?
Socket welding only requires inserting one pipe into the connecting end of another pipe, and the connection can be completed through welding. The overall connection point is solid and has a strong bearing capacity, providing a good guarantee for the operational safety of the pipeline. In addition, socket welding is also suitable for the connection of pipelines made of various materials and is applicable to various occasions.
What is butt welding?
Butt welding, as a high-precision connection method, achieves a high-strength, aesthetically pleasing and stable connection by subjecting the ends of two pipes of the same diameter to heat treatment and then combining them after heating. Its weld seam is uniform and smooth, without protruding foreign objects, making the bearing capacity and leak-proof performance of the connection more superior. It is especially suitable for occasions with high requirements for aesthetics.
It is a common welding joint for high-pressure pipelines. High technical proficiency is required during welding. However, it has a tight connection and good leak-proof performance, making it suitable for high-pressure and high-temperature environments. It is mainly used in the connection of pipelines with relatively small diameters.
Main differences between socket welding and butt welding.
1.Connecting method.
- Socket weld: after the pipeline is inserted into the socket, a fillet weld is performed, and there is an assembly gap of 0.8-1.6mm.
- Butt weld: the end faces of the pipelines are directly butted and welded. It is necessary to machine the bevel (such as V-shaped/U-shaped) in advance to achieve full penetration.
2.Strength and applicability.
- Socket weld is only used for pipelines with a diameter less than or equal to DN50, and it is not suitable for working conditions with severe vibration or thermal cycling (stress concentration is likely to occur due to the gap).
- Butt weld has higher strength and is suitable for high-pressure/high-temperature working conditions (such as ASME B31.1 Class 1 pipelines).
3.Inspection and cost.
- Socket weld has a low installation cost. There is no need for bevel machining, and it is suitable for scenarios where space is limited.
- Butt weld requires 100% RT/UT inspection, while socket weld usually only undergoes surface inspection (PT/MT).
4.Standard basis.
ASME B31.3 clearly distinguishes the applicable scopes of the two, and butt weld is the preferred option.
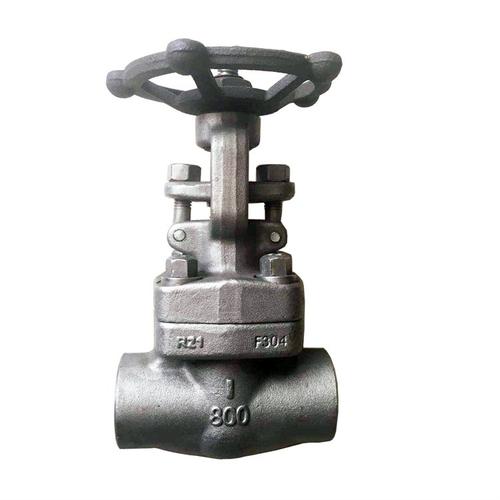
Socket weld vs buttweld: pros and cons.
Socket weld.
1.Advantages.
- It requires fillet welding which is easy to achieve.。
- Especially suitable for small diameters working at relatively high pressures.
- No preparation required other than cleaning the surfaces.
- Suitable for different materials.
2.Disadvantages.
- Strength and stress resistance is reduced due to limited weld penetration in the fillet.
- Not suitable for systems with fluids sensitive to contamination or reaction with the welding.
Butt weld.
1.Advantages.
- High strength and stress resistance which makes it suitable for high operation pressures.
- Suitable for large diameters and small diameters with high wall thickness.。
- Suitable for different materials.
2.Disadvantages.
- It requires a higher level of welding skills to be performed.
- It requires beveling the ends for proper weld penetration.
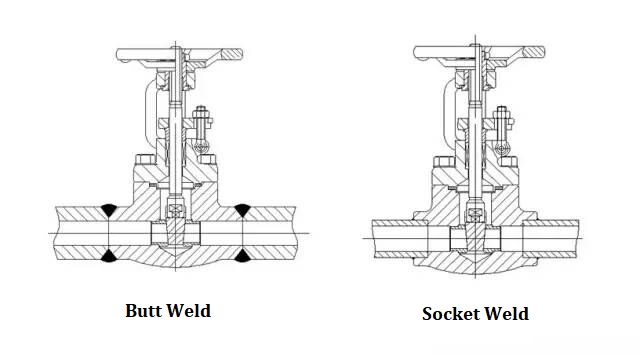
Butt Weld vs Socket Weld
Welding connection between valves and pipelines.
Valves and pipes are always “hand in hand”. The main connection types between valves and pipelines include flange, welding, wafer, threaded, clamp, and sleeve, etc. The way how valves are connected to pipelines or equipment cannot be ignored, as most of the leakage issues (such as running, emission, dripping, and leaking) in valves occur at these connection points.
Welding connection valves inculde butt welding valve and socket welding valve. Standards such as GB/T 12224, API 600, and ASME B 16.34 specify the requirements for welding bevel preparation of valves and pipelines. In practice, socket welding does not require bevel preparation and can be directly welded, whereas butt welding requires creating a 30-37.5° bevel on pipes with normal wall thickness.
- (1) Butt welding connection: both ends of the valve body are machined into butt welding bevels according to butt welding requirements, which correspond to the welding bevels of the pipeline, and are fixed to the pipeline through welding. Butt welding connection is applicable to various sizes of valves, working pressures, and high-temperature working conditions.
- (2) Socket welding connection: both ends of the valve body are machined according to socket welding requirements, and connected to the pipeline through socket welding. Socket welding connection is generally suitable for valves with ≤ DN50.