Case of an Accident Caused by Valve Fracture Resulting in a Major Leakage
Valves are one of the common devices used in both industrial and daily life. Different types of valves have different characteristics and application scenarios. Knowing that about various valve types can help us better select and use valves, improving the operational efficiency and safety of equipment.
Accident Caused by Valve Fracture
On one date of one year, a valve in an oil depot of an oil company fractured, resulting in the loss of more than 1,560 tons of gasoline. Since the location was in the Gobi Desert China, all the leaked oil seeped into the ground.
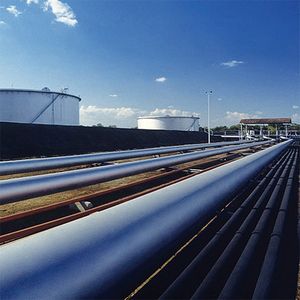
(I) Basic Situation
The oil depot is 2.9 km away from the petrochemical plant, connected by two underground pipelines with a diameter of D/V200, and these pipelines cross two roads. There is a flat cover-type valve well at each end of the roads. On December 9, 1981, the oil depot signed an oil transportation agreement with the refinery, and the measurement of the oil tanks in the refinery was taken as the basis for handover. The storage section chief in charge of oil transportation selected two young workers from the oil pump house to patrol the pipeline and arranged two telephone operators to answer the phones; the measurement team leader arranged the measurement work. The operation was carried out in two shifts from 9:00 to 19:00. The first shift was from 9:00 to 15:00. Oil transportation started at 12:00 (the oil temperature was -4.7 °C). The oil level in the tank before oil intake was 277 mm. At 13:45, the liquid level was 607 mm, an increase of 330 mm; at 14:40, the liquid level was 1,204 mm, an increase of 597 mm. The second shift took over at 15:00. At 15:50, the liquid level was 1,626 mm, an increase of 422 mm, and at 16:45, the liquid level was 1,964 mm, an increase of 338 mm. The oil intake speed began to decrease after 15:00. After hearing the report of the abnormal oil transportation situation, the leader of the oil depot instructed the storage section chief to check. The section chief said, “I know,” but actually did not check. Later, he left his post for personal reasons and did not return until 23:00. At 15:00 on the 10th, the section chief and a measurer went to the refinery for measurement and found there was a problem. Only then did they arrange two young workers to patrol and inspect the pipeline. When they patrolled to the second road 500 m away from the oil depot, they found that the valve in the valve well had fractured by 3 cm, and the oil leaked from this place and seeped into the ground.
(II) Analysis of the Causes and Lessons (Mainly Analyzed from the Aspects of Valve Quality and Selection)
This is a mechanical accident caused by valve fracture (a technical accident), and in essence, it is a serious accident due to negligence of duty. The main lessons are as follows:
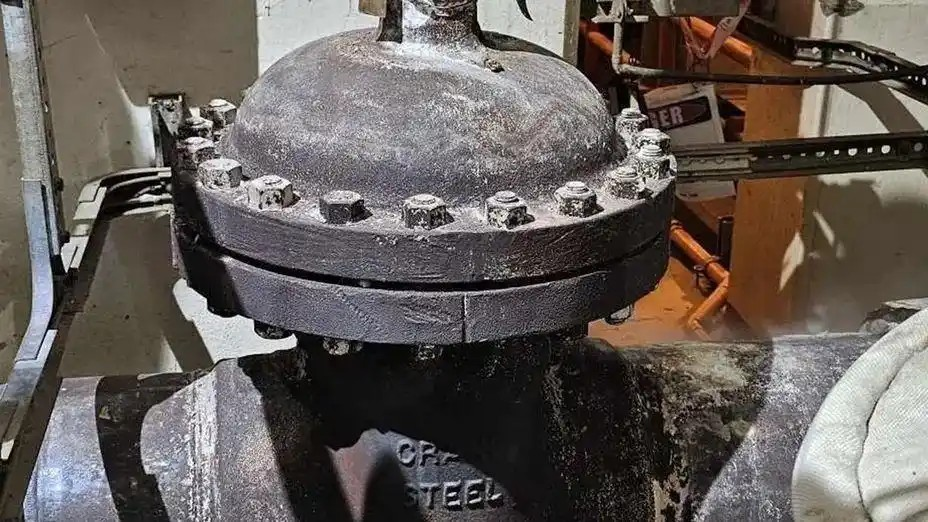
- Poor Valve Quality
For the valve body of the valve in the accident, there were cracks in 3 out of the 4 reinforcing ribs, all of which were perpendicular to the direction of the tensile force. According to the national technical standards for cast iron valves, they should be able to withstand a breaking tensile force of 337 tons, the valve bolts (M2012) should be able to withstand a breaking tensile force of 229 tons, and the pipeline (Φ219) should be able to withstand a breaking tensile force of 201 tons. That is, under the action of the breaking tensile force, the steel pipe should be the first to break, followed by the 12 bolts, and then the valve. Through the tensile strength test of this batch of valves (a set of three test bars), the values were 8.0, 8.5, and 8.5 kg/cm² respectively, which is 8.3 times less than the national standard of 20 kg/cm². Through sampling, testing, and analysis, it was found that the contents of sulfur and carbon exceeded the regulations, and the contents of silicon and manganese were less than the regulations, resulting in a decrease in the tensile strength.
After the accident, the oil depot inspected 70 DN200 valves, among which the reinforcing ribs of 12 valve bodies had cracks; 8 out of the 38 valves in the oil pump house had cracks in the valve bodies; and 5 out of the 8 valves in the oil pipeline outside the depot had cracks in the reinforcing ribs of the valve bodies. Poor valve quality is the main cause of this accident. - Design Issues
Generally speaking, there are not many problems in the design. However, from the perspective of management, some useful lessons should also be drawn from the design. For example, for the underground pipelines outside the oil depot, the designed covering soil depth was 8.5 m, without considering the uneven terrain factor. After the project was completed, the covering soil depth in some sections was less than 8.5 m. The valves for oil inlet and outlet of the oil tanks and the valves in the valve wells should be medium and high-pressure cast steel valves, but in fact, all the designed valves were - . The valve wells are of the flat cover type, without inspection rooms and steps, making it difficult to check the valve conditions during actual operation; in the valve wells, if some compensatory measures were taken, even if the valve quality was poor, it might not necessarily fracture; even if it fractured, it would not have a crack as wide as 3 cm.